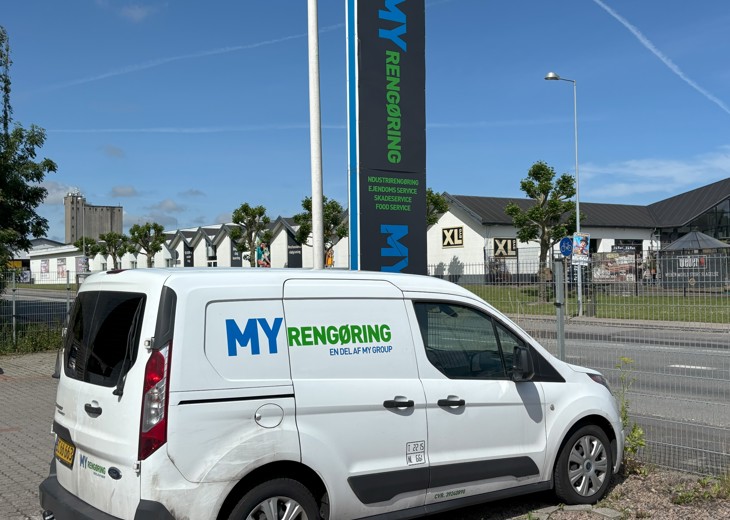
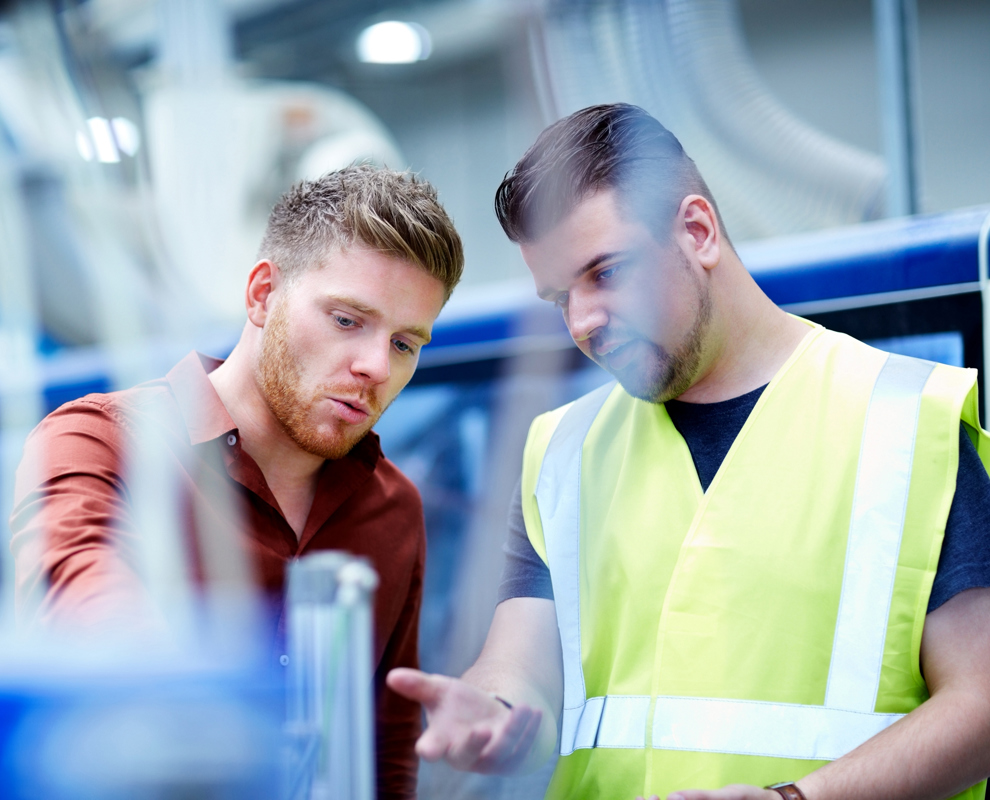
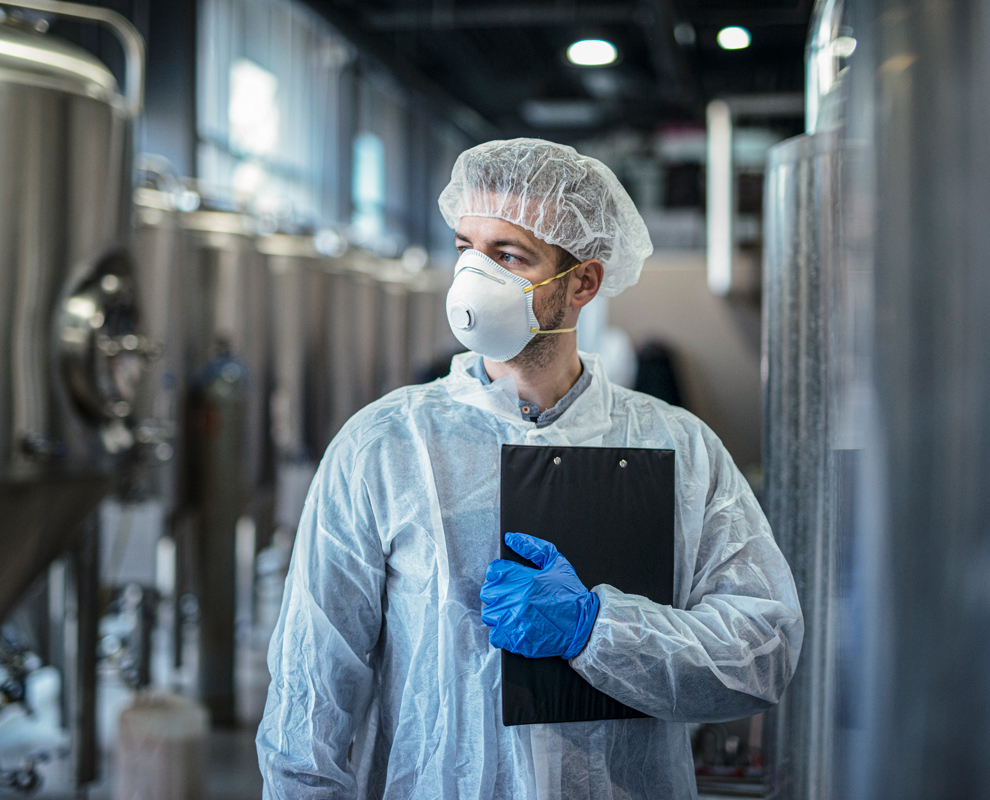
Foamico's low-pressure systems compared to traditional high-pressure solutions
-
40%Reduction in cleaning time
-
60%Reduction in energy consumption
-
25%Reduction in water waste
Tips for Conveyor Cleaners
When designing an automated conveyor belt cleaning system, the correct placement of nozzle bars is essential for effective cleaning. It is recommended that nozzle bars are installed on both the outside and inside of the conveyor system to achieve thorough range coverage and ensure that all surfaces are efficiently cleaned. In order to optimize the placement and functionality of these nozzle bars, it can be extremely beneficial to provide detailed pictures or videos of your conveyor setup.
These visuals will help provide an assessment of the conveyor systems and belt surface, allowing for tailored advice on the best positions for the nozzle bars. With this information, you can improve the performance of the cleaning system to ensure it meets your specific needs and achieves optimal results.
The only information one of our specialists needs to create a proposal and quote for the automation of the conveyor cleaning is:
-
Width of the Conveyor belts
-
The minimum distance the Nozzlebar needs to be from the Conveyor belts
-
Which products are transported?
-
Which system is available for the Rinsing and Foaming?
-
How long does it take for a full turn of the conveyor belt?
-
Do you want a Full automatic or Semi-Automatic system?
Automatic Conveyor Belt Cleaning System
Conveyor belt cleaning in the food industry is often a challenging, time-consuming, and labor-intensive task. However, implementing an automated conveyor belt cleaning system offers significant benefits. Not only does it improve the working environment by reducing manual labor and minimizing exposure to harsh cleaning chemicals, but it also results in significant time and cost savings. Automation increases the range of cleaning efficiency, ensures consistent sanitation, and reduces downtime, ultimately leading to a more streamlined operation and efficient productivity.
Consistent results:
Automated cleaning solutions reduce the risk of black spots and ensure a consistent cleaning result.
Time savings:
Reduced downtime: Automated solutions relieve cleaning personnel of time-consuming and tedious tasks, allowing them to focus on other tasks while the conveyor is being cleaned.
Cost savings:
Reduced labor costs and maintenance costs: Allowing staff to focus on other tasks instead of time-consuming conveyor cleaning reduces the overall need for manual belt cleaners.
Reduced water and chemical usage: Implementing an automated low-pressure conveyor cleaning solution saves significant amounts of water and chemicals compared to high-pressure alternatives.
Environmental benefits:
Reduced water consumption: Low-pressure cleaning solutions can reduce water consumption by up to 50% compared to high-pressure solutions.
Extended equipment life: Low-pressure cleaning technology is gentler on conveyor systems and electrical equipment. This reduces wear and extends equipment life.
Testimonial & Case Studies
Testimonial & Case Studies
Foamico Newsletter
Sign Up Today
Want to see what we can do for you?