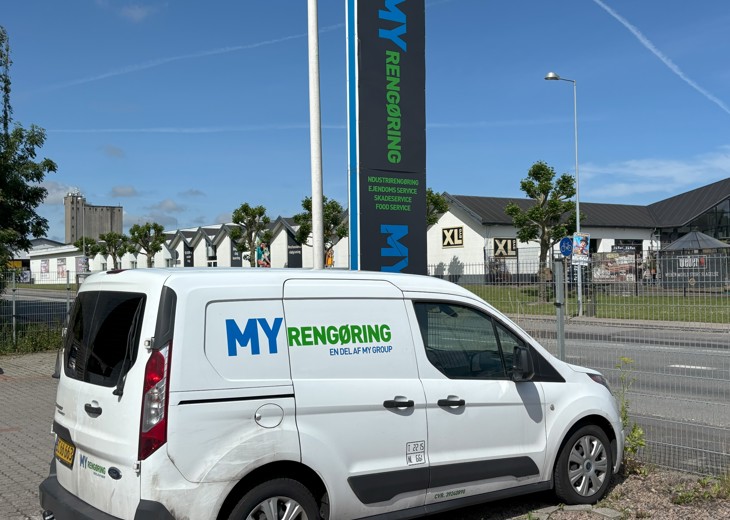
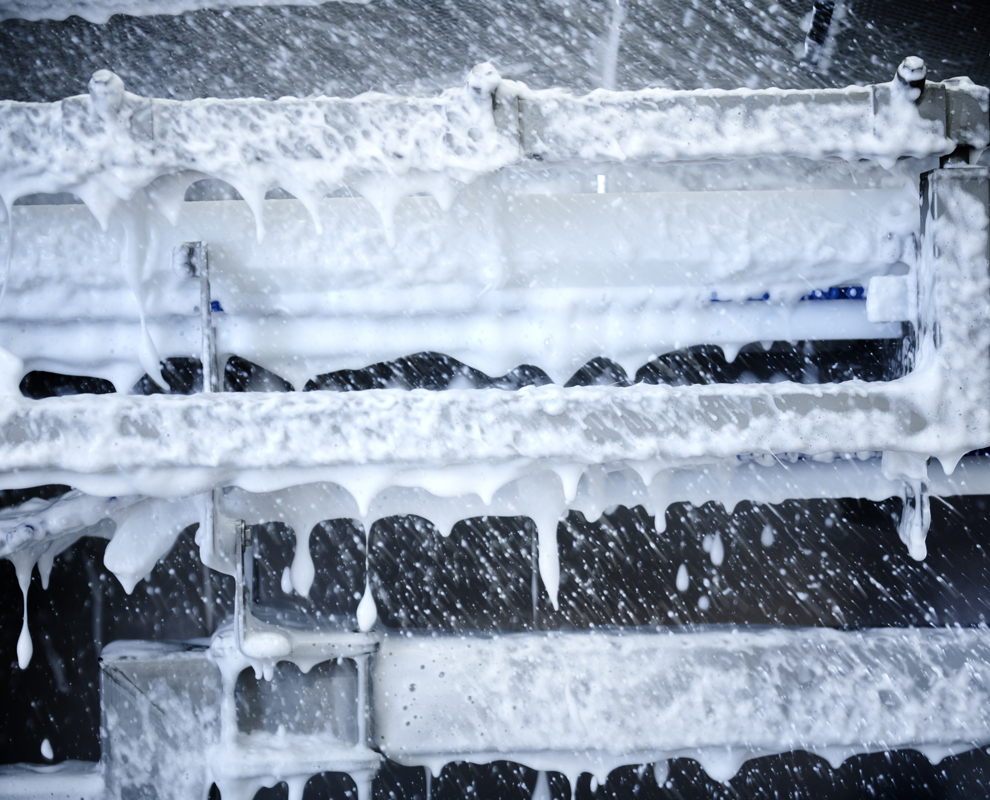
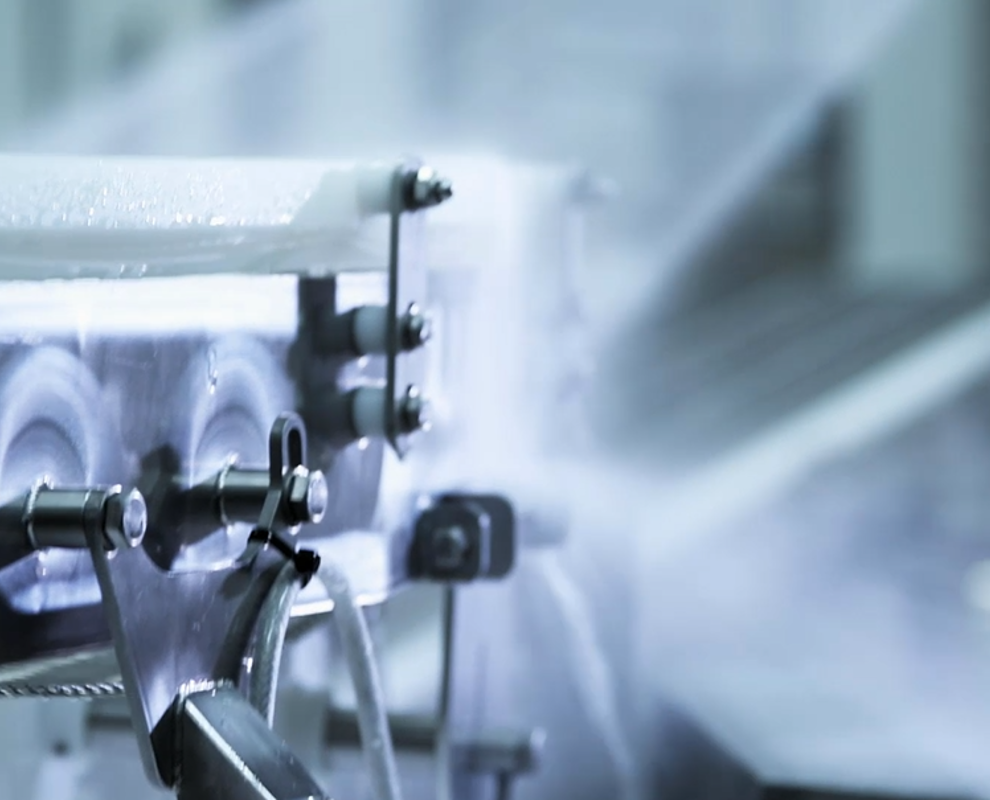
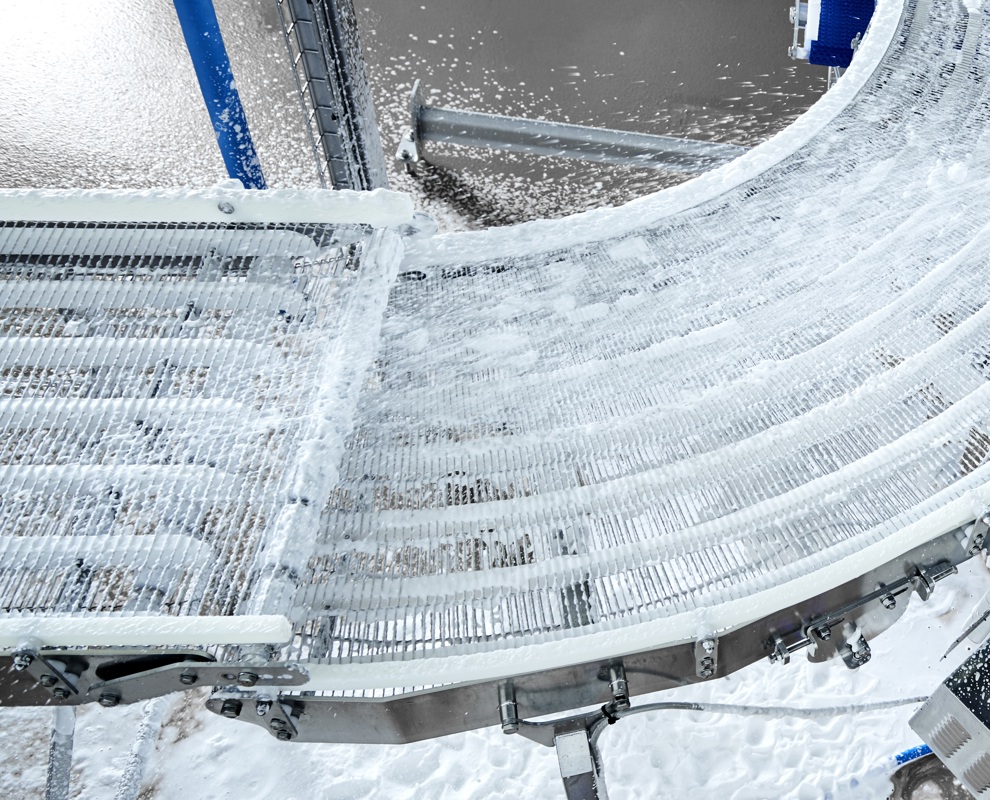
Benefits of Automated Conveyor Cleaning
-
1.Improved cleaning Efficiency
Consistent Results: Automated cleaning solutions reduce the risk of black spots and ensure an unvarying cleaning result.
-
2.Time Savings
Reduced Downtime: An automated cleaning system releases the cleaning staff from time-consuming and tedious tasks, allowing them to focus on other tasks while the conveyor is cleaned.
-
3.Cost Savings
Reduced labor costs: Reduces the overall need for manual labor by allowing staff to focus on other tasks rather than time-consuming conveyor cleaning.
Reduced water and chemical usage: Implementing an automated low-pressure conveyor cleaning solution saves significant amounts of water and chemicals compared to high-pressure alternatives. -
4.Environmental Benefits
Lower water consumption: Low-pressure cleaning solutions can reduce water consumption by up to 50% compared to high-pressure solutions.
Extended equipment life: Low-pressure cleaning technology is more gentle on conveyor components and electrical equipment. This reduces wear and extends equipment life.
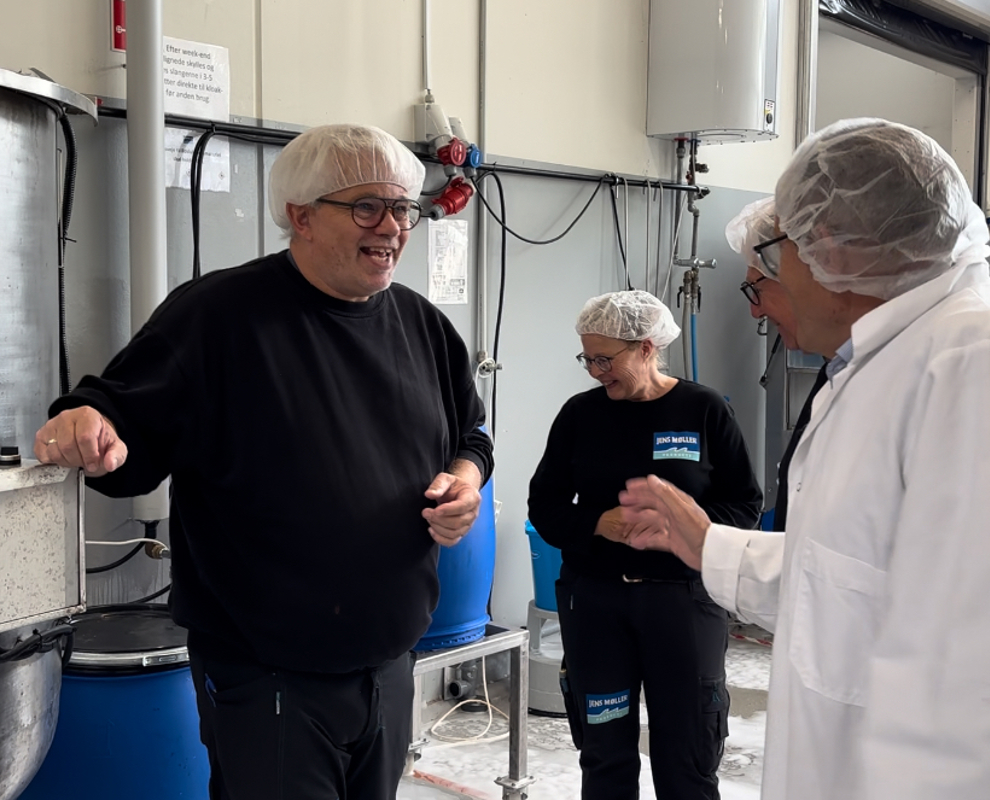
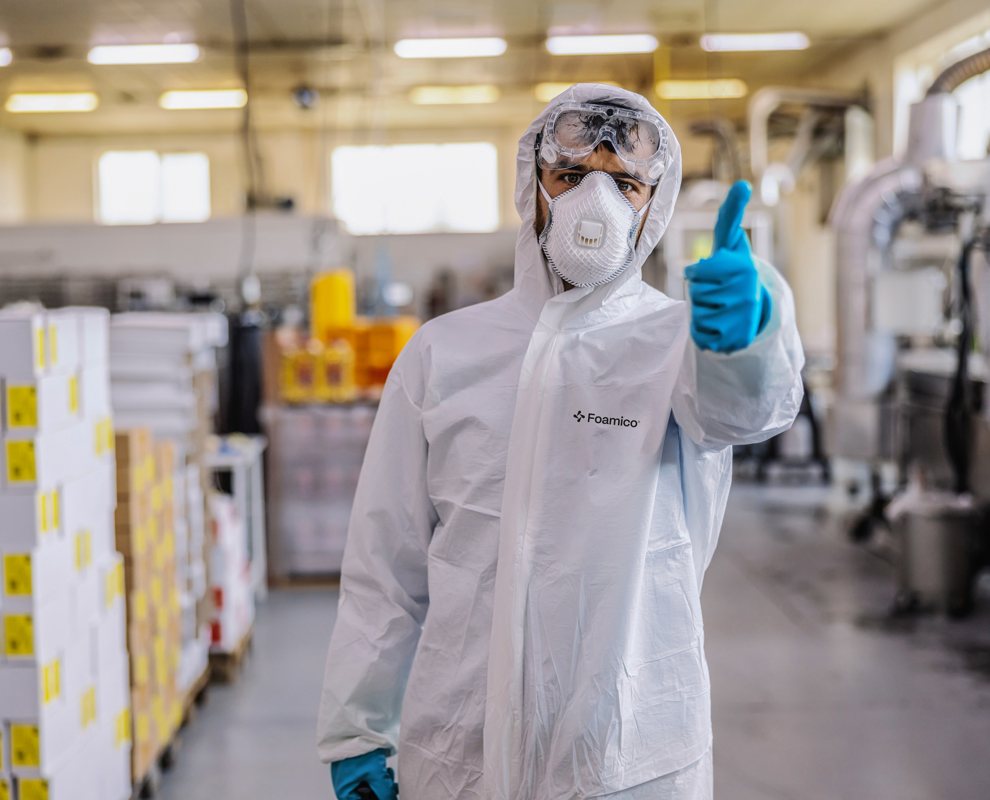
-
Automated CleaningAutomatic cleaning can decrease the time spent on cleaning, reducing water- and chemical usage and releasing cleaning staff from long and tedious cleaning steps. Automatic cleaning thereby reduces the environmental impact of the cleaning process significantly.See solutions
-
ConveyorConveyor belts are used extensively in the food and beverage industry to move products through processing plants, from raw materials to finished products. Automating these processes with conveyor belts significantly increases efficiency and safety.See solutions
Testimonial & Case Studies
Testimonial & Case Studies
Foamico Newsletter
Sign Up Today
Want to see what we can do for you?